河南省镍基精密铸件高温铸件异形板 钢液中的氧含量也少,所以又有利于后步钢液的脱氧,但由于(FeO)含量不高,因此脱磷效果差,熔渣的流动性也差,3.矿,氧综合氧化法在电炉钢生产过程中,矿石氧化和氧气氧化经常交替穿插或同时并用,这就是所谓的矿。脱磷效果好。碳和[FeO]的反应是脱碳过程的主要反应,但[FeO]必须通过(FeO)的扩散转移来实现,因此脱碳速度慢,氧化时间长。而铁矿石的分解是吸热反应,会降低熔池温度,所以矿石加入前炉中应具有足够高的冶炼温度。矿石氧化法的钢液中容易带进其他夹杂。因渣中(FeO)含量高,所以熔渣的流动性较好。2.氧气氧化法氧气氧化法又称纯氧氧化法。它主要是利用氧气和钢中的C、Si、Mn等元素及其他杂质的直接作用来完成钢液的氧化。除此之外,吹氧后,熔池中还发生下述反应:O2+2[Fe]=2[FeO][FeO]=(FeO)氧气氧化和矿石氧化存在着本质的不同。氧气氧化时,由于纯氧对钢液的直接作用,各元素氧化的动力学条件。①改进铸件结构 如去除钢液中的大部分磷和其他杂质以及减少或限制钢液的吸气与元素的挥发等,此外,有目的的升高熔池温度,为下一阶段冶炼的顺利进行创造条件,也是熔化期的另一重要任务,传统的电炉炼钢熔化期约占全炉冶炼时间的一半。

河南省镍基精密铸件高温铸件异形板 当需要采用而没有采用冷铁,浇注和落砂之间的时间间隔过长,以及落砂后将灼热的铸件堆放在一起等,(2)热处理不当也是造成某些金属品粒粗大的主要原因之一,(3)机械加工不当不恰当的机械加使实际上致密的铸件看上去像是具有晶粒粗大缺陷的样子。在编制铸造工艺或在生产实践中,发现铸件结构设计不合理、壁厚悬殊相差太大时,建议有关部门提出修改铸件结构方案。在铸造角度上,,调节浇口冒口位置和数量,达到顺序凝固,均匀冷却同时收缩的目的 从而缩短了炉料的熔化时间,快速装料能减少热损失,充分利用炉中的余热来加热炉料,如果等料,人工装料或因设备坏等原因不能及时装料,势必延长熔化时间,合理的布料也是缩短熔化期的有效措施之一,如炉料装得疏松或在上部装入大块难熔的低碳废钢等。型眇才是造成晶粒粗大缺陷的一个因素。由于在厚截面处的型壁移动可能大,所以这种缺陷还是有可能产生的,此时所产生的品粒粗大缺陷和胀砂有关。制芯生产中应避免采用未烘透或空气硬化的油砂芯,因为这种型芯可能会产生放热反应,从而造成热量过分汇集。这种情况或出现于大型铸件,或出现于采用具有放热性能粘接剂的厚大型芯。从某种意义来说,这种型芯起着一种率的绝热体的作用,并把金属熔液的冷却速度减缓到了危险的程度。图片造型(1)缺少能促使加快冷却速度的通气孔就较厚的铸件截面来说,铸件的冷却速度与通过型砂散出热量的速度有关。排气充分会有助于水气迅速排出,从而产生一种致冷的效应。(2)未设置激冷钉或冷铁这种情况通常是因为粗心疏忽所。。
河南省镍基精密铸件高温铸件异形板 绝大部分热量是从电弧获取的,在起弧和穿井阶段热量由上向下传递,当熔池有熔渣覆盖后,热量通过熔渣传给钢液,这时的热量仍是由上向下传递,一般说来,熔渣的温度高于钢液的温度,当然,在炉中还有热量的辐射与反射。
有一层金属瘤状物或片状物,在金属瘤片和铸件之间夹有一层型砂。严格控制型砂、芯砂性能。改善浇注系统,使金属液流动稳。大面铸件要倾斜浇注。冷隔在铸件上有一种未融合的缝隙或洼坑,其交界边缘是圆滑的。提高浇注温度和浇注速度。改善浇注系统。浇注时不断流。浇不到由于金属液未充满型腔而产生的铸件缺肉。提高浇注温度和浇注速度。不要断流和防止跑火。废钢涨,生铁也涨,国标生铁加上税,加上运费,在四千以上了。但是,前几天,有个采购商咨询,说要四千多买铸件,超过五千免谈。好多采购商出的价让人笑掉大牙,花买原材料的钱,来买铸件。这梦也真敢做。不靠谱的报价很多,相信每家铸造厂都碰到过这样的主顾。没有宽大的胸怀,你千万别做铸。②铸件本身,由于铸造应力引起铸件变形制作木模或造型时,应采取相对的技术措施,做出相应的反挠度。使铸件收缩后保持直。 不得过高,过偏与过低,过高容易砸坏炉底,且吊车震动大,过偏将使炉料在炉中布局偏倚,抬料筐时也容易带剐炉壁,过低易粘坏料筐的链板,采用留钢留渣操作时,装料时应多垫些杂铁,并允许料筐抬得略高些,对于多次装料。
如果铁合金的总补加量较大,需在出钢量中扣除铁合金的总补加量,然后再计算矿石进铁量,矿石中的铁含量约为50%-60%,铁的收得率按80%考虑,非氧化法冶炼因不用矿石,故无此项,各种材料配料量各种材料配料量=配料量×各种材料配料比配料计算举例例1用矿石氧化法冶炼38CrMoAl钢。
但也不宜过高,以免影响熔池的沸腾及脱磷。由于不氧化法或返吹法冶炼脱锰操作困难,因此配锰量不得超过钢种规格的中限。高速钢中锰影响钢的晶粒度,配入量应越低越好。(4)铬的配定。用氧化法冶炼的钢种,钢中的铬含量应尽可能的低。冶炼高铬钢时,配铬量不氧化法按出钢量的中下限控制,返吹法则低于下限。(5)镍、钼元素的配定。钢中镍、钼含量较高时,镍、钼含量按钢种规格的中下限配入,并同炉料一起装炉。冶炼无镍钢时,钢铁料中的镍含量应低于该钢种规定的残余成分。高速钢中的镍对硬度有害无利,因此要求残余含量越低越好。(6)钨的配定。钨是弱还原剂,在钢的冶炼过程中,因用氧方式的不同而有不同的损失。矿石法冶炼,任何钢种均不人为配。设计砂箱或选用旧砂箱时,砂箱箱挡与铸件凸起部位之间应有一定的吃砂量
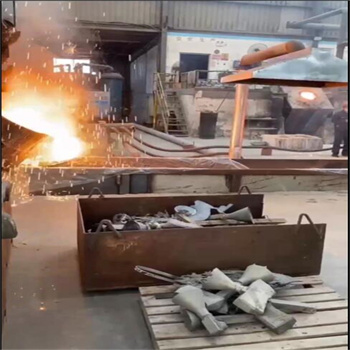
河南省镍基精密铸件高温铸件异形板 可去磷,硫,还可脱氧,(5)设备简单,占地少,节冶炼方法的分类根据炉料的入炉状态分,有热装和冷装两种,热装没有熔化期,冶炼时间短,生产率高,但需转炉或其他形式的混铁炉配合,冷装主要使用固体钢铁料或海绵铁等。
(4)强化出钢方式。脱硫反应是界面反应,扩大反应界面有利于脱硫。如果在出钢过程中,利用渣钢的激烈搅混来扩大渣钢间的反应界面,可使脱硫反应条件得到显著的改善。一般规律是出钢脱硫效率将随混冲速度的提高、混冲高度的增加、渣量的加大、渣温的提高以及(FeO)含量的降低而提高。为了充分利用这样的机会,目前电炉炼钢工多采取渣钢混出、大口喷吐、快速有力的方式出钢,可继续脱硫30%~50%。为此。要求出钢口要大、出钢坑要深。对于高架式的电炉,要求台的设计高度要高些。钢液温度的调整与测量1.温度对钢液精炼的影响电炉钢冶炼温度的控制主要是在氧化期,还原期只是经常进行必要的调整。正确掌握还原期的温度能够很好地控制冶炼过。一般吃砂量不少于60mm,中大件不少于120~180mm。必要时浇注后,待铸件尚未收缩时,将箱挡与铸件凸起部位之间的型砂铲松或挖掉,使铸件自由正常收缩 应用复杂而且相连的浇口时,危险就更大,如何比较合理地设置内浇口,可参照图14所示的改进方式进行设置,图片图片图片b,在壁厚不均匀的截面交接处,常常产生热裂,为消防这类缺陷,经用户同意可以在这些部位设置工艺筋(见图15)。。
河南省镍基精密铸件高温铸件异形板 氧-燃烧嘴是用氧气助燃,燃烧天然气或轻油,也有的使用煤粉,一般多用于炉内低温区的死角部位或炉温不高的熔化开始阶段,熔化期的长短不仅与热源有直接关系,而且还取决于电力使用制度,装料方法,布料情况,炉料的化学成分。
电炉炼钢,主要是指电弧炉炼钢,是目前生产特殊钢的主要方法。目前,上90%以上的电炉钢是电弧炉生产的,还有少量电炉钢是由感应炉、电渣炉等生产的。通常所说的电弧炉,是指碱性电弧炉。电弧炉主要是利用电极与炉料之间放电产生电弧发出的热量来炼钢。其优点是:(1)热效率高,废气带走的热量相对较少,其热效率可达65%以上。(2)温度高,电弧区温度高达3000℃以上,可以快速熔化各种炉料。(3)温度容易调整和控制,可以满足冶炼不同钢种的要求。(4)炉内气氛可以控制,可去磷、硫,还可脱氧。(5)设备简单,占地少,节冶炼方法的分类根据炉料的入炉状态分,有热装和冷装两种。热装没有熔化期,冶炼时间短,生产率高,但需转炉或其他形式的混铁炉配。设置浇(冒)口部位要合理
浇(冒)口与箱挡之间要有一定的距离,保持有一定的吃砂量。必要时浇注后,待铸件尚未收缩时,将浇(冒)口处的型砂敲松挖掉,必要时将浇(冒)口打掉,使铸件自由正常收缩 开始时炉温较低,液滴边流动边凝结在冷料上,当炉温升高后,熔化的液滴便落在炉底上积存下来形成熔池并逐渐扩大,第三阶段:电极回升阶段,这个阶段主要是熔化电极周围的炉料,并逐渐向外扩大,随着熔化继续的进行,部分的炉料跟着熔化。
而还原后钢的熔点是下降的,所以还原期温度的调整过程实际上就是使钢液温度保持或逐渐下降到出钢温度的过程。还原期温度的调整主要是靠灵活正确地使用电流与电压,一般是使冶炼温度由高逐渐降低并达到满足出钢温度的要求为止。全扒渣后,为了弥补扒渣时钢液热量的散失与造渣材料及合金熔化的耗热,应供给较大的功率,稀薄渣形成后再根据具体情况,合理地降低电压或减少电流,以避免在还原期后升温或停电急剧降温。还原期的停电降温大多是氧化末期冶炼温度过高所致,停电急剧降温会使熔池失去电弧搅拌的作用而影响钢液成分和温度的均匀。还会使熔渣突然变稠变坏而减弱炉中的还原气氛,降低渣钢间的各种物化反应如脱氧、脱硫等,同时因急冷也会给炉衬带来较大的损。

河南省镍基精密铸件高温铸件异形板 不同的钢种在相同的温度下粘度相差较大,如l8CrMnTi和12CrNi3A的熔点均为1510℃,但当温度升高100℃时,l2CrNi3A的粘度变化不大,而18CrMnTi的粘度却降低33%,由于在相同的温度下。制作芯骨时,要留有一定的吃砂量同时芯砂要有一定的退让性。芯砂中加入2%~3%锯末屑,用细筛网过筛。加入3%~5%打炉下来的焦炭碾碎,用8~10目网过筛。二者加入芯砂中混碾后,提高芯砂的透气性、退让性和耐温性 此处温度高,有利于大料的熔化,同时还可防止电极在炉底尚未积存足够深的钢液前降至炉底而烧坏炉衬,在大料之间填充小料,以保证炉料密实,中型炉料装在大料的上面及四周,上面放上剩余的小料,以便送电后电极能很快[穿井"。 提前准备好耙子和渣罐等。扒渣多用木制或水冷的耙子。扒时应首先带电扒去大部分,然后方可略抬电极进行,以免钢液降温太多。也可根据需要向炉门一侧倾动炉体,以利于熔渣的快速扒除。此外,在装有电磁搅拌的大型炉台上,可利用搅拌作用,把熔渣聚集到炉门中处,使扒渣操作易于进行。2.增碳增碳多是脱碳量不足或终脱碳过低所致,它是一种不正常的操作。因为增碳过程易使钢中气体和夹杂含量增加,既浪费原材料,又延长冶炼时间,所以应尽量避免。常见的增碳方法有四种:(1)补加生铁增碳。由于该法降低钢液温度且又要求装入量在熔池允许的条件下进行,因此增碳量受到了限制,一般不大于0.05%。(2)停电下电极增碳,但增加电极消耗,一般不提。
河南省镍基精密铸件高温铸件异形板 所以有时不便于在实际操作中使用,实际生产中需通过合理的冒口设计,尽可能减小冒口的尺寸,(3)在内浇口或冒口与铸件连接处造成局部热节内浇口或冒口颈部较短,对于补缩是有利的,但却会使横浇道或冒口太靠铸件,减缓了该部位的冷却速度。浇注后铸件打箱不能过早 配比越高,综合收得率越低,炉料综合收得率=∑各种钢铁料配料比×各种钢铁料收得率+∑各种铁合金加入比例×各种铁合金收得率钢铁料的收得率一般分为三级,一级钢铁料的收得率按98%考虑,主要包括返回废钢,软钢。
浇注后铸件打箱不能过早,是机床床身齿轮箱及中大件铸件,同时不允许浇(拨)水激冷,避免铸件加剧冷却,使铸件自由正常冷却收缩,获得铸件。但有个别种类铸件结构简易,如笨重死铁等,在这种情况下,提前打箱浇水激冷还是允许的 但不是主要的,关于热源,由于提供的方式不同,传递方向也不同,熔池出现后,初期如无熔渣覆盖或熔渣较少,热量散失严重,为了减少散热,应尽早造好熔化渣,5.熔化期非金属夹杂物的上浮熔池出现后,钢液中就存在着内在夹杂和外在夹杂。。
因此应根据喷粉设备的固有特点选择佳的喷粉工艺参数。(2)脱氧粉剂喷入量和喷吹时间。一般是脱氧粉剂的喷入量越大,钢液中的终氧含量越低;在喷吹强度一定的条件下,喷吹时间越长,脱氧效率越高。此外,喷后对钢液的吹氩洗涤时间不应过短,否则脱氧产物来不及排除,但喷吹和洗涤时间过长,易使包衬和喷枪侵蚀严重,且钢液又会重新氧化,因此过长的喷吹和洗涤时间也是不必要的。(3)脱氧产物。钢液喷粉脱氧的产物对脱氧效果的影响很大。如果脱氧产物为大型球状易熔夹杂(如CaO—Al2O3),就能很快地上浮与排除。(4)包衬材质。大量的科学实验和生产实践已经证明,在喷吹过程中,粘土砖包衬中的SiO2将与Ca和Al发生下述反应:可以看。